
La fabricación de plásticos PET (Tereftalato de polietileno) requiere compresores de aire especializados: compresores de pistón para PET. Estos compresores de pistón son ampliamente utilizados por los productores de botellas plásticas para fabricar botellas y empaques para industrias como la de bebidas, alimentos y cuidado personal
Aplicaciones de los compresores de aire en la fabricación de botellas PET.
Compresores de aire para moldeo por inyección de botellas PET.
El moldeo por inyección consiste en inyectar plástico termoplástico o termoestable fundido en una cavidad de molde cerrada utilizando aire comprimido generado por compresores de tornillo o compresores de pistón. Tras la solidificación, se forma el producto final.
En el moldeo por inyección, los compresores de aire de pistón se utilizan para tareas como la limpieza de equipos, la expulsión de moldes, la formación de piezas asistida por aire, el inflado de tubos, el moldeo por vacío/presión y la operación de cilindros.
La tecnología de aire comprimido es compatible con la mayoría de los termoplásticos y materiales de ingeniería (por ejemplo, PS, HIPS, PP, ABS).
El éxito del moldeo por soplado depende de un flujo de aire estable y limpio a presiones predefinidas. Los compresores de pistón para PET que suministran aire de alta presión de manera constante garantizan la producción en una sola operación de piezas plásticas complejas, de dimensiones precisas o con inserciones metálicas.
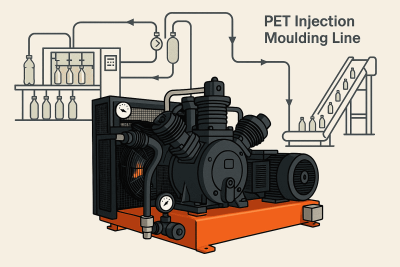
(Compresores de aire para el moldeo por inyección de botellas PET)
Compresores de aire para el moldeo por soplado de botellas PET.
El proceso de moldeo por soplado de botellas PET implica calentar las preformas, cerrar los moldes, formar por estiramiento y soplado, dar forma después del soplado, abrir el molde y desmoldar. El aire comprimido se inyecta en las preformas calentadas para expandirlas hasta la forma deseada de la botella PET.
Los compresores de pistón para el moldeo por soplado de PET son equipos auxiliares críticos en la producción de empaques PET, y se aplican ampliamente en industrias como bebidas, aceite comestible, condimentos, lácteos, licores, cerveza, productos farmacéuticos y productos químicos de uso diario.
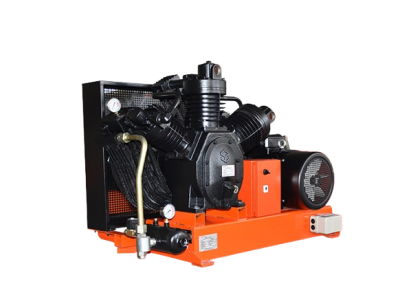
(Compresor de aire de pistón)
Entendimiento de los requisitos clave.
Seleccionar el modelo adecuado de compresor de pistón requiere evaluar varios factores para cumplir con las necesidades operativas específicas.
Determinar la demanda de aire.
Tasa de flujo: Volumen de aire requerido por minuto (m³/min o L/min).
Presión: Varía según la aplicación.
Aplicaciones comunes y requisitos:
Aplicaciones |
Rango de presión |
Tasa de flujo (Operación) |
Moldeo por inyección de preformas |
6–8 bar |
Baja a Media |
Moldeo por soplado
|
30–50 bar |
Alta |
Actuadores /robots neumáticos
|
6 - 10 bar |
Baja |
Enfriamiento por aire |
6–10 bar |
Media |
Cálculo de la tasa de flujo requerida.
La demanda total de flujo (m³/min) = Σ (Consumo de equipo individual × Cantidad) × Factor de simultaneidad × (1 + Factor de fuga) × (1 + Factor de expansión futura).
Parámetros:
Consumo de equipo individual: Consulte los manuales de equipo o estándares de la industria (por ejemplo, 0.5–5 m³/min para máquinas de inyección).
Factor de simultaneidad: 0.6–0.9 (más bajo para más equipos).
Factor de fuga: 10%–20%.
Factor de expansión futura: 10%–30%
Selección de tipos de compresores de aire.
Tipo de compresor de aire |
Caracteristicas |
Compresor de pistón de una etapa |
Presión máxima ~10 bar; adecuado solo para moldeo por inyección |
Compresor de pistón de dos/tres etapas |
Presión de hasta 30–50 bar; ideal para moldeo por soplado de PET |
Compresor de aire lubricado |
Duradero y eficiente; requiere tratamiento de aire (filtros/deshumidificadores). |
Compresor de aire libre de aceite o exentos de aceite |
Adecuado para producción de grado alimenticio. |
Sistemas de post-tratamiento compatibles.
El aire de alta calidad es crucial para la claridad, resistencia y seguridad alimentaria de las botellas, por lo que es esencial configurar equipos de post-tratamiento para su compresor de pistón PET para garantizar un aire comprimido puro y limpio.
Enfriador de salida: Reduce la temperatura del aire de salida.
Secador: Elimina la humedad (desecante o refrigerado).
Filtros de linea: Eliminar el aceite (coalescentes), el polvo (particulado) y los olores.
Normas de calidad del aire (ISO 8573-1):
Partículas: Clase 1.
Agua: Clase 4 (punto de rocío ≤ +3°C).
Aceite: Clase 1 (≤0.01 mg/m³).
Consideraciones de eficiencia energética.
Los compresores de aire representan entre el 30% y el 50% del consumo energético de una planta de botellas plásticas.
VSD (Variador de velocidad): Ajusta la salida según la demanda.
Motores de alta eficiencia (IE3/IE4).
Sistemas de recuperación de calor: Reutilizan el calor residual para agua del proceso.
Planificación de escalabilidad y redundancia.
Asegúrese de que sus compresores de pistón PET puedan manejar:
Demanda máxima: Durante la alta producción.
Expansión futura: Incluir una capacidad adicional del 10% al 20%.
Respaldo/Redundancia: Mantener la producción durante el tiempo de inactividad de la unidad principal.
Mejor práctica: Utilizar varios compresores más pequeños con controles inteligentes (en lugar de una unidad sobrada).